Ressources dossier
BioeconomyConstruction potential of biobased materials
According to the UN, building construction was responsible for 37% of global CO2 emissions in 2021, underscoring the industry’s extremely high levels of energy consumption and pollution. Thus, transitioning towards biobased materials could provide a promising way for the industry to reduce its environmental footprint. We explore this important topic below.
Published on 16 February 2023
Extraction and transformation of materials, intensive construction, energy-greedy activities and performance... in France and worldwide, the building construction industry (see below) is a key source of pollution. According to the French Ministry of Ecology, Sustainable Development, and Energy, this industry is responsible for 43% of the country’s annual energy consumption and 23% of its greenhouse gas (GHG) emissions. The construction and demolition phases engender the highest energy costs and are responsible for 60-90% of the total carbon footprint of a building with a 50-year life span. “Yet, these figures do not take into account the impacts of material extraction, transport, and processing”, underscores Laurent Arnaud, head of the Sustainable Construction Department at the French Centre for Studies on Risks, the Environment, Mobility, and Urban Planning (CEREMA). Cement production alone emits nearly one billion tonnes of CO2 because raw materials such as clay and limestone are transported thousands of kilometres and must be heated to 1,450°C during cement creation.
A shift in regulatory focus
In 1974, the French government passed its first regulations related to thermal standards in occupied buildings, which sought to limit energy usage tied to heating, air conditioning, water heating, and lighting. As of January 1, 2022, new regulations (RE 2020) are in place that focus on environmental impacts: attention is now paid to the GHG emissions resulting from building construction, which are estimated using a life cycle analysis (LCA) of the materials used. This shift thus strongly encourages manufacturers to opt for lower-emission materials. For example, hemp concrete could serve as a green alternative to conventional concrete, with its energy-intensive production and large carbon footprint. With this recent legislation, the French government is pursuing the environmental transition objectives of the country’s Climate Action Plan1, which is aiming for carbon neutrality by 2050.
Biobased materials, a promising alternative
The French government has a three-pronged strategy: lowering energy consumption, billable energy costs, and carbon footprints for existing and future buildings. The goal is to promote the more frequent use of wood and biobased materials, which store carbon over a building’s lifetime.
Taken directly from the living world, biobased construction materials have various forms. They may be the fibres used in insulation or the granules with which mortar is made. The source material may be wood, hemp, cork, or flax, to name a few examples.
INRAE researchers have been exploring these and related topics for over 15 years. “Such materials, and especially their fibres, could serve as simple replacements for petroleum-based materials”, explains Monique Axelos, INRAE’s Scientific Director of Food and Bioeconomy. “However, they also present their own advantages, such as lightness and strength, and can thereby contribute to the circular economy, boosting sustainability and regional development.” These materials have tremendous potential, since LCA shows that they can help drastically reduce GHG emissions. They can even store carbon. “A 1-m², 30-cm-thick hemp concrete wall can store 32 kg of CO2 over its lifetime”, comments Laurent Arnaud. Another advantage of this approach is that it makes use of “waste”, plant matter that is generally discarded, such as straw mulch or rice hulls (i.e., the protective coverings of rice grains). Furthermore, it can be procured at a low cost almost anywhere in France.
Facilitating progress
At first glance, such materials would appear to be an easy sell. However, as Philippe Léonardon, an engineer in ADEME’s Construction Department, explains, “At present, only 10% of insulation materials on the market in France is biobased.”
He clarifies that what is lacking is political commitment because the necessary technical knowledge already exists. Indeed, Philippe Léonardon highlights that the new legislation does not require construction companies to use biobased materials. In his view, the regulations only indirectly encourage the use of such materials because the underlying calculations are complex: “Each construction product, piece of equipment, and service, such as the supply of energy or water, is assessed from the perspective of a specific environmental objective. Overall GHG emissions are determined using 27 indicators, which include the relative contribution to global warming, consumption of fresh water resources, and elimination of radioactive waste. Thus, while biobased materials can help meet environmental objectives, they are not specifically named.”
France is the leading producer of hemp in Europe and can therefore reliably develop hemp-based construction materials. Such will not be the case for other countries that do not have consistent access to this crop. While biobased materials are a promising source of solutions, we must carefully consider how to scale up their production to ensure that the entire value chain is sustainable. Monique Axelos warns that we must be wary of certain unconscious biases. For example, people might not value biobased products because the latter are assumed to be biodegradable, given that they are natural. She comments, “To optimally utilise resources, we need to manufacture long-lasting, reusable materials.” It is also essential to assess the impacts of harvesting plant residues, which naturally fertilise soils, and to maintain reasonable transport distances. Furthermore, resources must be managed so as to avoid competition among industries. For example, grain straw already serves as animal bedding and is used to produce biogas via anaerobic digestion and second-generation liquid fuel in biorefineries.
1. Launched in April 2022, the Climate Action Plan is a set of official economic and budgetary measures intended to guide French industry through the environmental transition (read it here in French).
2020 Thermal standards: Multiperformance biobased materials
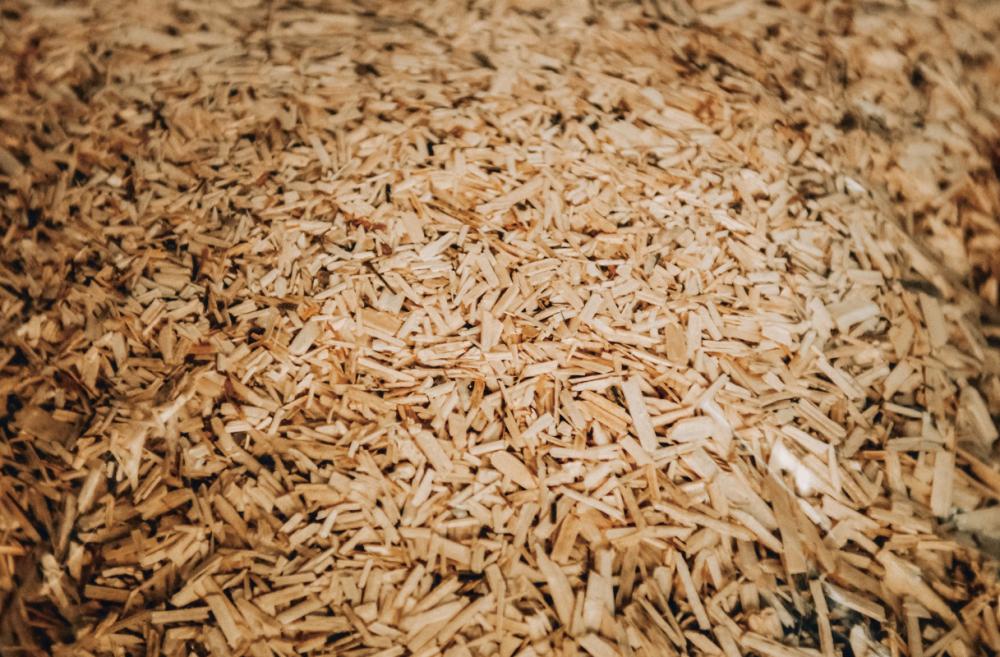
“Insulation is 80-90% air.”
Biobased materials are not the most suitable solution for structures such as bridges or dams, where robustness is crucial. However, for less demanding projects, such as offices or residences, biobased materials display desirable engineering traits, such as lightness and flexibility. They also possess other valuable characteristics, which largely result from their dense air pockets. “Plant-based materials are very porous and thus absorb water vapour from the air. As a result, they can act as a sort of reservoir and help to regulate building temperature in the summer”, explains Laurent Arnaud. He confirms that suitable plants can be found in every region of France. Thermal lag is a key property of construction materials. When thermal lag is higher, exterior heat takes longer to pass through the walls and into the building. As a result, biobased materials readily comply with new environmental regulations stating that, for a residence to be habitable, interior temperatures cannot exceed 25°C, even in hot weather.
In the winter, the material’s porosity leads to excellent levels of insulation. The pores are the plant’s former xylem and phloem. “Insulation is 80-90% air. So, we are essentially selling people air, which is excellent at insulating buildings”, concludes Laurent Arnaud. Plant fibres, with their honeycomb structures, outperform conventional materials when it comes to soundproofing. As a result, plant biomass is a 2-in-1 material, mediating both temperature and noise. Finally, when properly designed, biobased products are recyclable; they can even be used as mulch. Such is not the case for conventional materials such as concrete or mineral wool (e.g., fibreglass). Thus, buildings constructed with biobased materials would generate very little waste at the end of their lifespans. In contrast, the building construction industry currently produces 46 million tonnes of waste per year in France. It would seem that biobased materials are ecologically sustainable. However, do they resist the test of time? To understand how plant fibres degrade over the longer term, research was conducted on linen fibres in 17th century canvases and 4,000-year-old Egyptian mortuary cloths by a scientific consortium that included INRAE. The results showed that damage was caused less by aging itself and more by the environmental changes (e.g., in temperature, humidity, UV exposure) experienced over time. Certain conservation techniques were also to blame. These issues must be considered when designing or utilising biobased materials.
Energy sobriety: A local approach to mitigating GHG emissions
“Using plant biomass, aka biobased materials, is certainly a step forward. However, we must also be looking at other ways of reducing carbon emissions”, remarks Isabelle Capron. She is an INRAE researcher and the head of the Biobased Materials Research Group, run jointly by INRAE and CNRS. Her colleague Bruno Duchemin (University of Le Havre-Normandie) voices the opinion of many scientists when he states that energy consumption must be reduced. He notes, “In 2019, research concluded that massively renovating buildings using straw could store 500 to 700 megatonnes of CO2 equivalents across the EU’s 28 member states over the next 200 years*”. Yet, even this ambitious and promising approach would only offset 60% of the annual CO2 emissions due to gas flaring by the oil industry. This practice involves burning the “waste” natural gas released during fossil fuel extraction and processing. Flaring is responsible for a tiny percentage of total GHG emissions from fossil fuels. It is clear that innovation can only take us so far. We must also lower our consumption.
“In our research, we are developing products and processes that are 100% biobased and biodegradable. They utilise waste from forestry systems, agricultural systems, and the food industry, such as brewer’s draff, apple peels, and walnut shells”, explains Isabelle Capron. She continues, “However, these resources are produced locally in small quantities. We are essentially talking about “niche” forms of storage. Moreover, transportation may become too expensive to be economically viable, especially in the case of waste-based innovations. We must therefore focus on the local scale, ideally within French cities.” Taken together, these findings underscore that our societies must adopt more circular economic systems, where production meets local needs and utilises less energy.
* From : Duchemin C., 2021. La biomasse : remède miracle pour le climat ? La Vie des idées.
-
Pierre Yves Lerayer
Author / Translated by Jessica Pearce