Ressources dossier
BioeconomyBuilding tomorrow: 9 biobased materials
Walls, floors, insulation materials, paints: more and more construction projects are utilising biobased materials. We take a closer look at 9 innovations that eschew non-renewable resources that were designed with the help of INRAE researchers.
Published on 16 February 2023
Fighting bacteria with cellulose
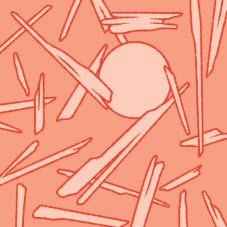
Industrial solutions are being developed that focus heavily on silver nanoparticles, which possess biocidal properties that can be used to protect various substances (e.g., surfacing, cellophane, paint) from microbial contamination. One major concern is that, over time, these nanoparticles tend to make their way into the environment, where they can negatively impact biodiversity. INRAE has been working with various public- and private-sector partners from the SERENADE Laboratory of Excellence to develop a process for reducing the levels of silver nanoparticles as much as possible in paints. Researchers are currently exploring the efficacy of cellulose nanocrystals produced by the paper industry, although other forms of plant biomass could potentially be utilised. Cellulose nanocrystals are completely natural and biodegradable. The silver nanoparticles attach themselves to the cellulose nanocrystals via a process that controls particle number, distribution, and size. The end result is twofold: not only does the product release minimal amounts of silver, but its biocidal properties are also greater than those of conventional paints thanks to the more even distribution of nanoparticles. INRAE patented this novel technique in 2020, and it could eventually be used to generate more environmentally friendly commercial products.
Hemp concrete, 35 years on
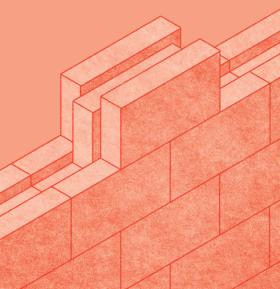
Hemp concrete was first used in house construction in 1986. Hemp shives are the fundamental ingredients in this biobased concrete. The shive is the woody core of a hemp stalk. It is stripped of external fibres and mixed with a mineral binder, most frequently lime. “For over 30 years, this type of hemp concrete has proven its effectiveness in various small- and large-scale construction projects in both rural and urban environments. Thanks to its excellent thermal and soundproofing properties, it plays an essential role in reducing energy consumption and increasing thermal comfort in homes”, states Bernard Kurek, a research director in INRAE’s Joint Research Unit for the Fractionation of Agroresources and the Environment (UMR FARE). “At times, there were serious issues, such as when the binder and the hemp shives did not set properly, which then had catastrophic consequences at construction sites. Since 2010, we have been collaborating with industry stakeholders and the French National School of State Public Works (ENTPE) in Lyon to better understand how to combine plant biomass and binders.” The key mechanisms at play within the hemp shives were identified during INRAE-funded doctoral research*, which was completed in 2013. Under certain conditions, the result is delayed binder setting, which leads to the above issues. This research can help drive work on other types of plant stalks that could serve the same function as the hemp shives. Since then, INRAE has formed a partnership with the private company Fibres Recherche Développement to improve the quality of hemp shives as well as that of other plant fibres. This focus makes sense, given that hemp is quite environmentally friendly: it requires little in the way of irrigation, inputs, or pesticides but absorbs as much CO2 per hectare as a forest.
* Diquelou Y., 2022. Interactions entre les granulats de chanvre et les liants à base de ciment et de chaux : Mécanismes de la prise et propriétés des interfaces formées dans les agrobétons. Thesis. University of Reims.
Cellulose as a superinsulator

For over 10 years, the INRAE Research Unit Biopolymers, Interactions, and Assemblies (BIA) has been exploring cellulose’s ability to stabilise emulsions. Normally, to mix two immiscible liquids, such as oil and water, it is necessary to use surfactants that might be harmful to the environment. BIA researchers have managed to replace the surfactants with cellulose nanofibres, which are a renewable and 100% biodegradable resource. One of this technology’s many possible applications is the creation of superinsulation. “For a given material, insulation properties can be enhanced by reducing density and pore size”, explains BIA Research Director Isabelle Capron, “Our methodology allows these characteristics to be fine-tuned.” The emulsion is stabilised exclusively by the cellulose nanofibres. After drying, it forms a rigid panel with impressive insulation properties; it outperforms both mineral wool and polystyrene. “We are still working to further improve resistance and better comply with current industry standards”, elaborates Isabelle Capron. The sole ingredients are water, oil, and cellulose.
Locally sourced, chemical-free wood siding
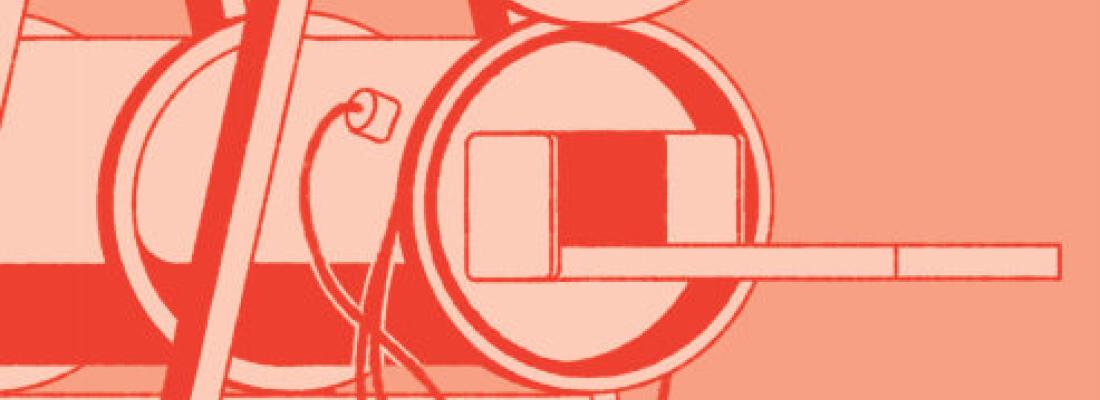
In 2021, the French building construction industry used 3.21 million m3 of imported softwood and 134,700 m3 of imported tropical wood. Figures suggest that 10% of French residences are built with imported wood. Work is underway to promote local wood production systems with small carbon footprints. In 2013, the Laboratory for Research on Wood Materials formed a partnership with the private company MSL Lorraine. Together, they developed the FURALOR process, which improves the technical performance of beech, a species that occurs naturally throughout Europe. The challenge is to make the wood more weather resistant, which would also improve its ability to repel fungi and microorganisms. If such could be achieved, beech could serve in outdoor applications, including in siding, noise barriers, garden furniture, or outdoor flooring. Preliminary work is being conducted to optimise the process depending on wood piece type.
Surfacing with antimicrobial properties
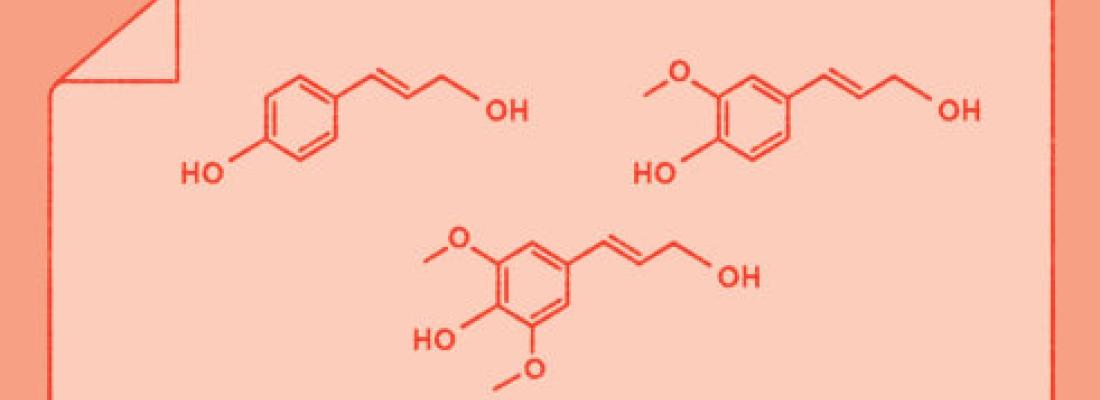
Imagine a future in which our windows are covered with an anti-UV film, or our walls and floors physically repel microbes? Lignins are chemical compounds that naturally occur in woody plants such as hemp and trees. These organic molecules are unique because they simultaneously display anti-UV, antioxidant, and antimicrobial properties. Scientists with the Joint Research Unit for the Fractionation of Agroresources and the Environment (UMR FARE) are looking to exploit these properties. They are conducting experiments in which they mix different types of lignins with a water/alcohol solvent and then apply the mixtures to various surfaces. They have been able to obtain surface films with the above desirable traits, which could lead to the development of biobased, antimicrobial paints or coatings. This patented technology has drawn the interest of the building construction industry.
Green epoxy: espousing natural resins
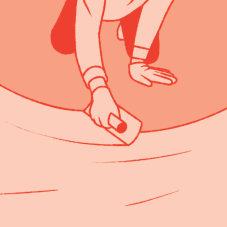
Transportation, chemistry, construction, and electronics... all these industries, among others, rely on epoxy resins. They are even to be found in the aisles of home improvement stores. A major concern is that most epoxy resins use bisphenol A, a particularly toxic compound. They also require the use of a hardener that is generally derived from fossil fuels. Between 2015 and 2018, the Green Epoxy project sought to develop entirely biobased resins. This work had a budget of €2.8 million and was the collaborative fruit of several industry and research stakeholders, including INRAE. The project generated epoxies using polyphenols (e.g., tannins), which are universal plant compounds, and specifically exploited by-products from the wood industry. INRAE continued pursuing the above research with Horizon Europe funding, in the form of the NoAW project. Several improvements were made to the hardeners, and different polyphenol sources were employed. Tannins can be extracted from grape marc rather than from wood. The former is a residue produced in large quantities by the wine industry. These 2 consecutive projects have highlighted that it is technically feasible to produce 100% natural, biobased epoxy resins. However, manufacturing costs remain higher than for chemical resins, which is an industrial barrier to the commercialisation of this technology.
Sunflowers and shellfish
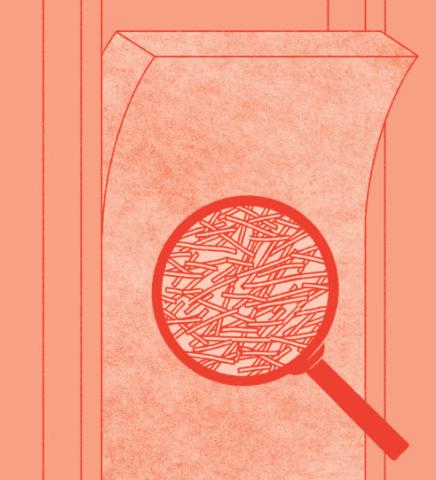
France is among the top producers of sunflowers in Europe: more than 700,000 hectares were sown in 2022. Once the plant’s precious seeds have been harvested, its stalks are most often left behind or sometimes burned. However, sunflowers are highly fibrous and thus display great physical resistance. They are also porous, which means they provide first-rate thermal insulation. These properties indicate that sunflower stalks could be incorporated into the insulation panels used by the building construction industry. Between 2011 and 2015, INRAE and its collaborators explored uses for this undervalued agricultural by-product as part of the Démether project. Sunflower stalks were ground down and then mixed with a chitosan binder. Chitosan is a compound found in the shells of crustaceans. Natural and biodegradable, this binder also possesses antibacterial properties. The Démether project gave rise to a prototype for insulation panels. Inexpensive to produce, they make use of previously unexploited agricultural residues. Several industry partners are seeking to parlay the project’s findings into commercial products. It is worth highlighting that public- and private-sector research alike is exploring the insulation capacity of other plant fibres.
For example, INRAE has begun looking at flax via the SINFONI Investments for the Future Programme. While flax-based panels display good thermal and soundproofing properties, their sensitivity to moisture means exterior applications remain impossible. Thus, the research continues. At present, 92% of industrially produced insulation is made from mineral wools, which present human health risks, or from cellular plastics, which are environmentally unfriendly. Consequently, plant-based insulation holds a great deal of commercial promise.
Turning waste to stone
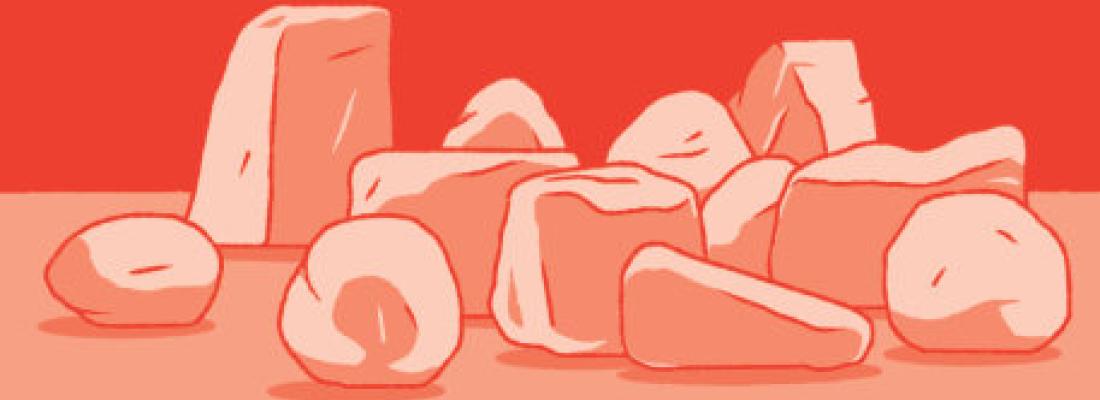
Some materials remain difficult to recycle. In France, around 40 million tonnes of non-recyclable waste is buried or incinerated each year. Launched via INRAE's 3BCAR Carnot Institute, the start-up Néolithe has identified an alternative solution: transforming the waste into stone. More specifically, rock fragments can be used as construction aggregates (e.g., as a road base or to make concrete). The waste is first crushed to form a fine powder, which is then mixed with water and a binder. The result is small stones that are 80% waste. Founded in 2019, Néolithe first focused on construction site waste (e.g., insulation, plaster, wood) before expanding to household and industrial waste. In 2022, the start-up announced it was opening an 11-hectare industrial site near Angers. By 2023, the company hopes to have 24 of its “fossilisation” units in place, which could treat up to 20 tonnes of waste per day. These ambitious objectives should respond to the arduous challenges we are facing.
2-in-1 mushrooms
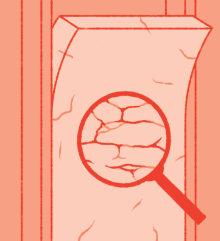
Filamentous fungi can proliferate within a few days’ time by binding together via their creeping hyphae. In 2019, researchers in the Laboratory for Agroindustrial Chemistry, the BFF Laboratory, and the Centre for Agroresource Application and Processing exploited this fungal property to produce biobased materials from agricultural residues (i.e., shavings). First, plant fibres were exposed to temperature and pressure treatments. Then, the resulting mixture was inoculated with a candidate fungus and cultured under controlled conditions. Once the process was complete, the resulting material contained a quantity of air that depended on initial fibre density. Materials with many air pockets displayed properties like those of polystyrene, which is used in packaging and thermal insulation. In contrast, materials with few air pockets were functionally similar to chipboard and could thus serve as replacements in short-term construction projects. This structure was achieved by fermenting and thermopressing the medium. In either case, the result is 100% biodegradable and can be used as agricultural fertiliser at the end of its life.
Networking for innovation: 3 questions for Coraline Caullet, project manager at the 3BCAR Carnot
Since 2011, collaborations have been proliferating between the private sector and the Carnot for Bioenergies, Biomolecules, and Biobased Materials from Renewable Carbon (3BCAR), which is run by INRAE. The aim is to produce sustainable innovations via ecodesign.
What are the Carnot?
The Carnot designation is granted to groups of researchers who carry out what I like to call research-to-business (RtoB) projects. Scientists and entrepreneurs come together to collaborate directly, in accordance with an ISO 9001 contractual protocol. Every four years, the French National Research Agency (ANR) re-evaluates whether a given group continues to meet the Carnot standard of excellence. This process ensures the groups’ continued research quality and boosts the number of contracts between Carnot and private companies.
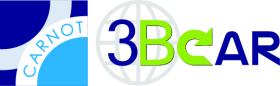
How does 3BCAR work?
Simply put, companies reach out to 3BCAR if they want to tackle a bioeconomy challenge. We put them in touch with researchers who can help them explore solutions by applying fundamental concepts. In addition, we annually fund projects, to the tune of around €1.2 million/year, that delve into potentially marketable, economically viable ideas. These projects help research move to the proof-of-concept stage, work that is protected by intellectual property rights (e.g., patent, know-how).
What is the strength of this approach?
At Carnot Institutes, scientists refine their skills by exploring innovative yet fundamental approaches, while industry stakeholders can avoid the risks intrinsic to this initial phase and focus on bringing a proven concept to life. 3BCAR draws upon the expertise of around 550 scientists across 18 groups and exploits the cutting-edge technologies represented across our 23 platforms. Manufacturers can ensure that their products or processes remain environmentally friendly at all stages of production. Technologies are often transferred to start-ups, who more readily accept potential risks and who thus serve an essential intermediary role in France’s R&D landscape.
-
Yann Chavance & Sarah-Louise Filleux
Authors / Translated by Jessica Pearce