Bioeconomy Reading time 3 min
Bioethanol: optimising wood pre-treatment for profitable production
PRESS RELEASE - Various complex processes enable the release of the sugars contained in wood, which are used in particular to produce second-generation bioethanol. Scientists from INRAE, the University of Reims-Champagne-Ardenne and the company Européenne de Biomasse have identified ranges of technological trade-off (temperature and pre-treatment time) that enable oak and poplar residues to be reclaimed while minimising the economic investment. The results were published on 03 December in the journal Applied Energy.
Published on 03 December 2024
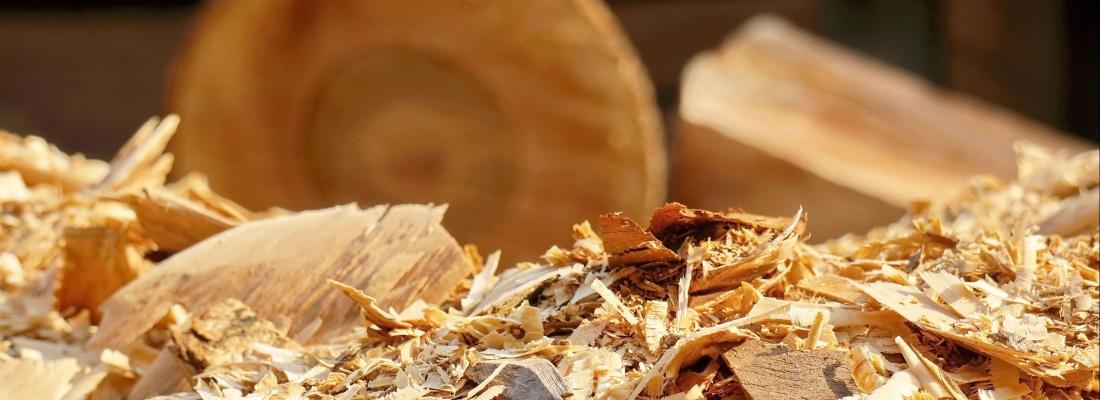
Wood residues represent a renewable resource for obtaining biomaterials or biomolecules of interest that can be used to manufacture a wide range of products such as fuels, solvents, surfactants. This residual biomass has the advantage of not competing with food or feed. But the complex structure of wood, rich in cellulose, hemicellulose[1] and lignin, makes it difficult to deconstruct using enzymatic catalysts in order to access the molecules of interest, and thus requires a pre-treatment stage.
Pre-treatment by steam explosion
Steam explosion consists of heating the wood sample after prior impregnation with water, followed by a rapid reduction in pressure which destructures the material. This pre-treatment method transforms the wood into an aerated fibrous form. The pre-treated wood can then be shaped to make pellets for heating (the current market for Européenne de Biomasse) or fractionated to release sugar (glucose molecules), which can be used to produce, for example, ethanol.
Pre-treatment by steam explosion has already proven its effectiveness in various industrial sectors, but remains very costly for the production of second-generation bioethanol: it represents 30 to 50% of equipment costs for the entire bioethanol production process and 20 to 25% of operational costs.
Taking this problem as their starting point, scientists from INRAE, the University of Reims-Champagne-Ardenne and Européenne de Biomasse set out to maximise ethanol production while at the same time limiting the cost of pre-treatment.
To carry out tests with 3 species of wood (oak, poplar and spruce), the scientists obtained supplies directly from the Européenne de Biomasse plant, located in the Grand Est region of France, which recovers wood residues from the region's forests for the manufacture of heating pellets. The wood chips collected were pre-treated by steam explosion, exploring different ranges of temperature and duration (10 contrasting conditions).
The results obtained have allowed to determine the optimal pre-treatment conditions for the three wood species and show that the ethanol production increases with the pre-treatment severity up to medium severity conditions and then becomes stable, demonstrating that the most drastic conditions are not the most appropriate ones to apply. Based on these data, and taking into account the specific yield ranges of the steam explosion process operated by Européenne de Biomasse, the scientists have succeeded in establishing scenarios for oak and poplar only, in order to optimise the pre-treatment stage and thus maximise bioethanol production, all while being economically viable.
Optimising bioethanol yields from oak and poplar
The species selection parameters were set with a lower limit for bioethanol yield at 85% of optimum value and a higher limit for economic investment at +25% compared with the least intensive pre-treatment.
The best trade-off for oak is about 15 minutes of pre-treatment at 198°C, with a bioethanol yield of 129 mg/g of dry matter and a 22% increase in economic investment. For poplar, it corresponds to approximately 10 minutes of pre-treatment at 205°C, with a yield of 111 mg/g of dry matter and a 16% increase in investment. Compared with optimum yields calculated without any economic criteria, this represents a very moderate reduction of 9% and 4% for oak and poplar respectively, while pre-treatment costs are reduced by 25 to 50%.
This study shows the possibility of optimising the pre-treatment and conversion of plant biomass, adapted to the industrial conditions of a company in terms of material and operational investment criteria, using the example of bioethanol. This method could therefore be easily transferred to the production of other products of interest derived from glucose, such as bioplastics or biosolvents.
[1] A complex sugar contained in the cell walls of plants and wood.
The Member States of the European Union have set the share of renewable energies to be used by 2030 at 42.5%, with a 5.5% share for advanced biofuels, biogas and renewable fuels of non-biological origin in the transport sector. https://www.europarl.europa.eu/factsheets/en/sheet/70/renewable-energy
Reference
Audibert E., Floret J., Quintero. et al. (2024). Determination of trade-offs between 2G bioethanol production yields and pretreatment costs for industrially steam exploded woody biomass. Applied Energy, DOI: https://doi.org/10.1016/j.apenergy.2024.125028